A range of innovative approaches to tackle the industry’s current and future skills challenges at all stages are being developed and piloted by the Automotive Industrial Partnership. This includes initiatives to encourage more young people to consider careers in the industry, support for upskilling, progression and the retention of talent in the sector:
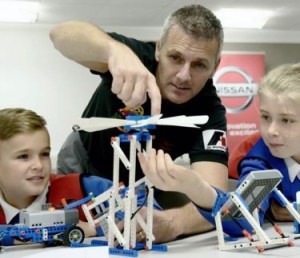
Basic Skills
Led by Nissan, the Automotive Industrial Partnership has introduced programmes to raise awareness of automotive careers with the aim of attracting more work ready new entrants to the sector.
Art of Manufacturing
Nissan launched the Art of Manufacturing programme to introduce nine and ten year olds to the world of manufacturing. The programme involves a full day visit to their manufacturing site and a project linked to the Year 6 curriculum.
The initiative was a new venture for Nissan in the UK and the Automotive Industrial Partnership has enabled the pilot to be scaled up. The programme and resources have been shared with other automotive businesses, such as Toyota in Derby who are now delivering their own version. The programme will run until at least 2018.
- Find out more about the Art of Manufacturing programme.
Industrial Cadets
Industrial Cadets is a programme championed by Nissan to encourage more 11-16 year olds to consider joining the automotive industry by highlighting the range of career opportunities available.
As part of the six day programme, students get to meet young graduates from different departments in Nissan, ranging from engineering to human resources. They also take part in a five day production simulation where two teams compete to set up a factory, develop and improve production methods and resolve quality issues. The programme, which will run until at least 2018, has proved to be extremely popular and the model has been shared with other manufacturers.
Apprenticeships
Automotive Apprenticeship Matching Service
The Automotive Industrial Partnership has developed the Automotive Apprenticeship Matching Service to redirect high quality talent from over-subscribed automotive apprenticeship programmes to other companies within the sector that have opportunities. By actively working with both employers and candidates the aim is to ensure that talent is harnessed and regained within the automotive industry.
The service has huge potential to benefit the automotive sector, as well as capacity to be up-scaled to help increase the number of apprentices in the wider engineering and other sectors.
- Find out more about the Automotive Apprenticeship Matching Service
- Watch our launch video
- Find out what it’s like to be an automotive industry apprentice
Upskilling
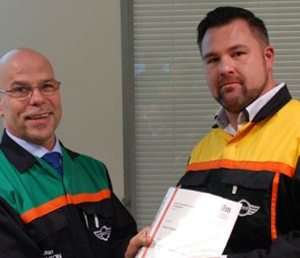
ProLead Management and Leadership Programme
Leadership skills were a key skills shortage area identified by the sector’s employers in a report commissioned by the Automotive Industrial Partnership.
Of particular importance is driving up skills in critical manufacturing leadership positions – which play a vital role in boosting productivity, quality and competiveness. As a result, BMW and JLR collaborated to develop ProLead on behalf of the industry.
The training programme, which is primarily aimed at existing managers in first line leadership positions, combines existing qualifications and tailors them to provide leaders with in depth management and technical knowledge. It has been developed using best practice from the Worldwide operations of UK based vehicle manufacturers and has proved to be so successful that formal accreditation is currently being sought.
Maintenance Upskilling
Ensuring that the UK supply chain is amongst the most competitive in the world is a priority for the Automotive Industrial Partnership.
Jaguar Land Rover supports this ambition and has led on the development of a maintenance up-skilling programme for its UK suppliers. The training programme is designed to increase capability in various maintenance skills, leading to process reliability improvements within the supply chain.
Since the 14 week programme began the results have been powerful, with participants from different suppliers showing an average improvement of more than 30% when tested at the end of the course.
New Growth Technologies
Problem Solving
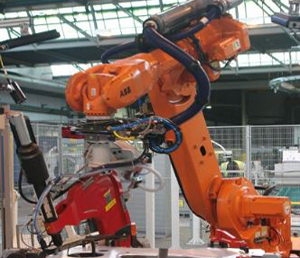
The rate of technological change in automotive manufacturing operations is accelerating. Ensuring the industry’s workforce can keep pace with this rapid growth and innovation is essential, using techniques such as advanced problem solving.
When reviewing the way training in this area was delivered, an inconsistency across the sector was identified.
This led to the development of the Advanced Problem Solving programme by Toyota Motor Manufacturing (UK) Ltd on behalf of the industry to introduce a standardised approach. It is aimed at engineers, as well as leaders and supervisors.
The majority of the companies that have taken part are component suppliers and it is estimated that each learner who has been on the programme has delivered an average of £35,000 in quality cost savings for their businesses. Formal accreditation for the programme is currently being sought.
- View the case studies for Stadco and Pektron, two of the organisations that have benefited from the programme.
Skills Funding Guidance
Navigating the skills funding system can be a challenge. To help employers, the Automotive Industrial Partnership has developed a detailed guide.
LDF OverviewLDF is a systemised methodology to create learning materials and solutions through phases of ANALYSIS, DESIGN and DEVELOPMENT. |
LDF GlossaryDefinitions for some of the phases from the Learning analysis, Design and development Framework |
Training ProgrammesInnovative approaches to tackle the industry’s current and future skills challenges at all stages are being developed and piloted by the Automotive Industrial Partnership |